Inventory Control: Avoiding Common Mistakes
Understanding Inventory Control
Effective inventory control is crucial for any business that deals with physical products. Without proper management, businesses can face overstocking, stockouts, and increased operational costs. This post will explore common mistakes in inventory control and how to avoid them.
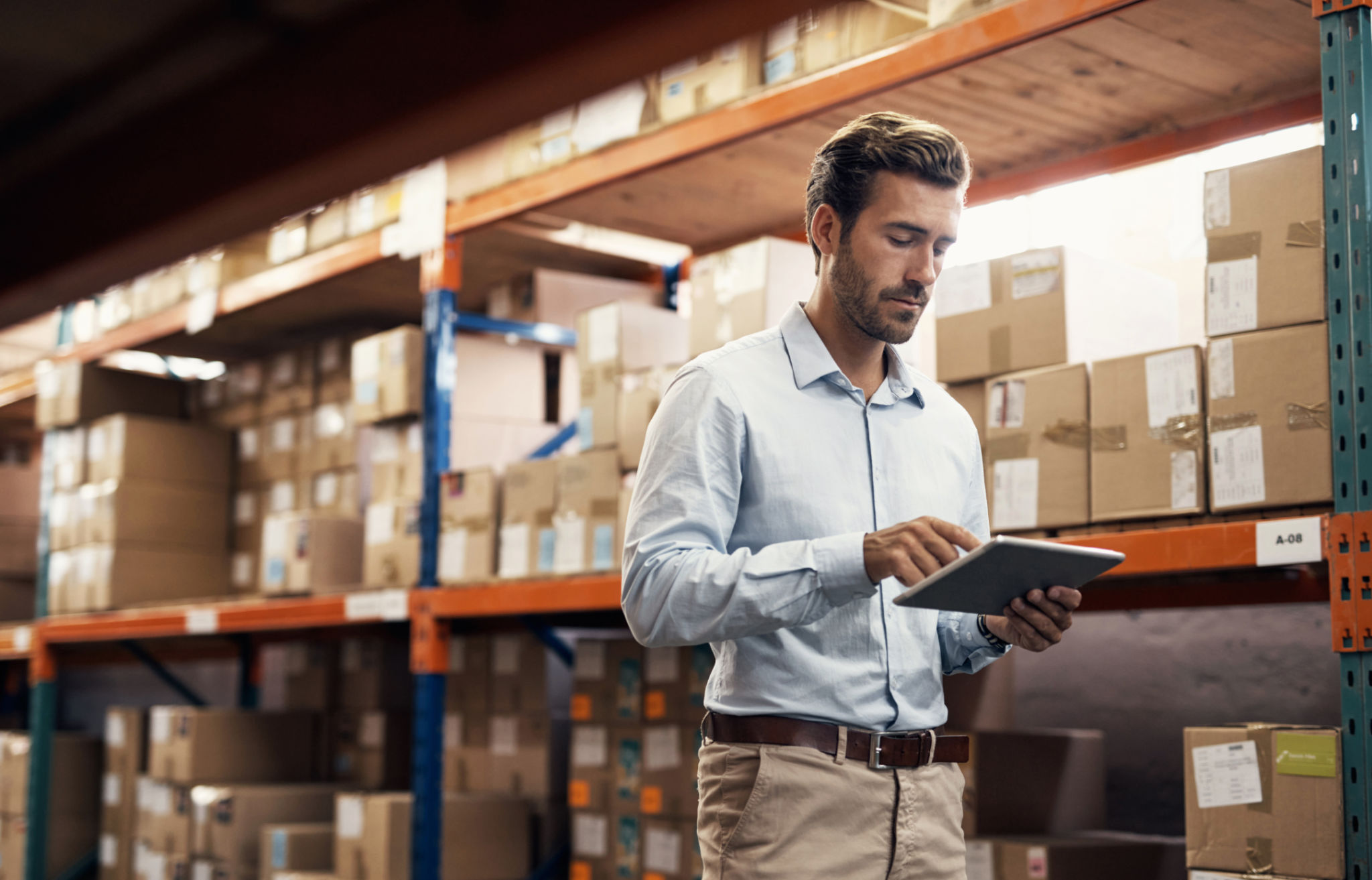
Lack of Regular Audits
One of the most frequent mistakes is failing to conduct regular inventory audits. Without them, discrepancies between actual stock and recorded quantities can go unnoticed, leading to inaccurate forecasting and planning. Implementing frequent audits ensures that the inventory data is up-to-date and helps identify potential issues before they escalate.
- Schedule periodic audits.
- Use technology to streamline the auditing process.
- Analyze discrepancies to prevent future occurrences.
Ignoring Demand Forecasting
Demand forecasting is essential for maintaining optimal inventory levels. Many businesses overlook this aspect, leading to overstocking or stockouts. By using historical sales data and market trends, businesses can predict future demand more accurately and adjust their inventory accordingly.
Invest in reliable demand forecasting software and regularly review the data to make informed decisions. This proactive approach can significantly reduce excess inventory and ensure product availability.
Poor Supplier Management
Another common mistake is inadequate supplier management. Relying too heavily on a single supplier or failing to maintain good relationships can lead to supply chain disruptions. Diversifying suppliers and maintaining good communication are key strategies for mitigating these risks.
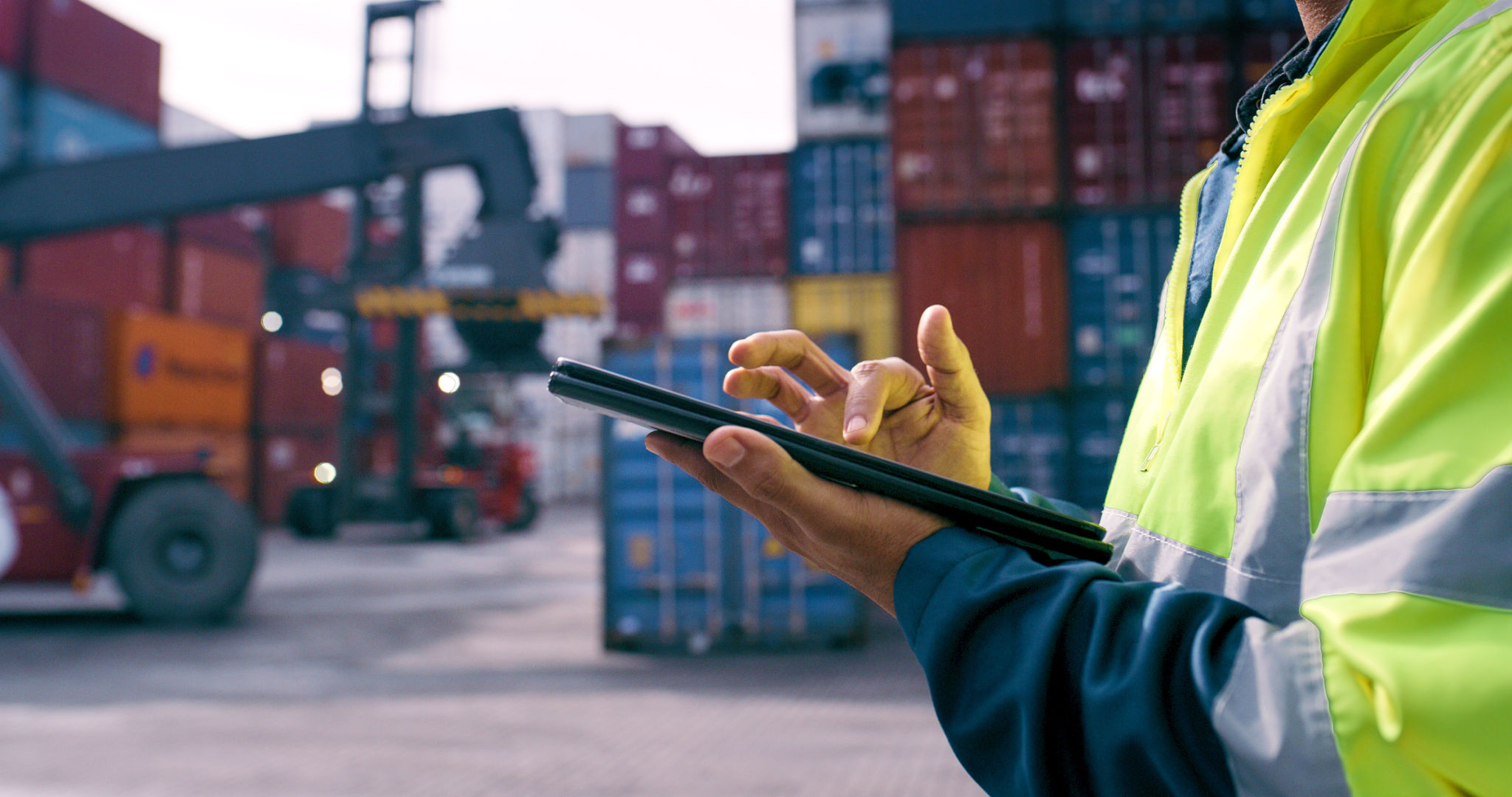
Neglecting Technology Integration
In today's digital age, technology plays a vital role in inventory control. Businesses that neglect to integrate technology into their inventory systems often face inefficiencies and errors. Automated systems can help track inventory in real-time, forecast demand, and even automate reordering processes.
Consider investing in an integrated inventory management system that suits your business needs. This not only saves time but also reduces human error, leading to more accurate inventory control.
Not Training Staff Properly
Even with the best systems in place, untrained staff can cause significant problems in inventory management. Ensuring that all employees involved in inventory control are properly trained is crucial for maintaining efficiency and accuracy.
- Provide comprehensive training sessions.
- Keep staff updated with the latest inventory practices and technologies.
- Encourage open communication for reporting issues.
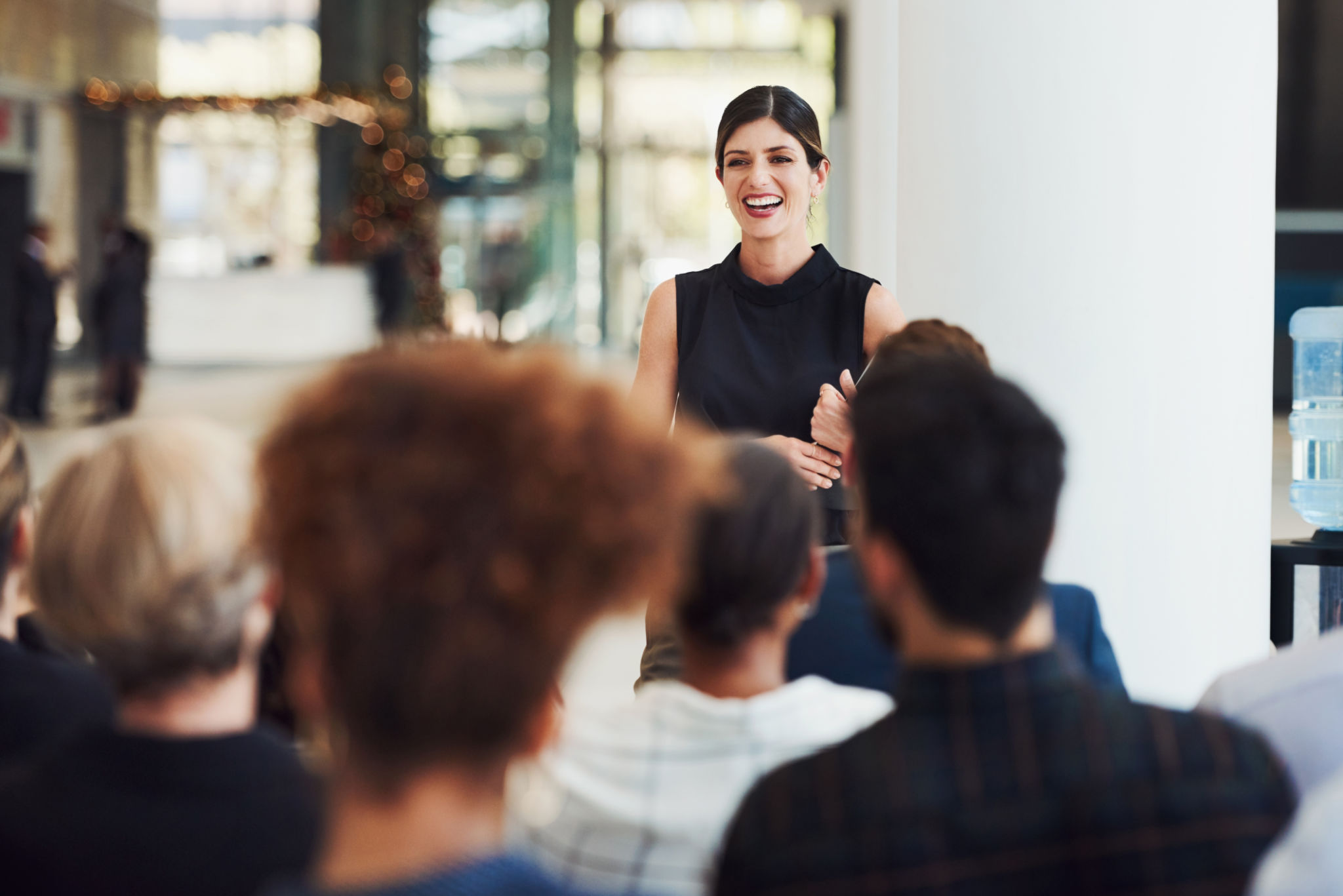
Conclusion
Inventory control is a critical aspect of any product-based business. By avoiding these common mistakes and implementing best practices, businesses can improve their inventory management processes, reduce costs, and enhance customer satisfaction. Regular audits, demand forecasting, supplier management, technology integration, and staff training are all key components of effective inventory control.